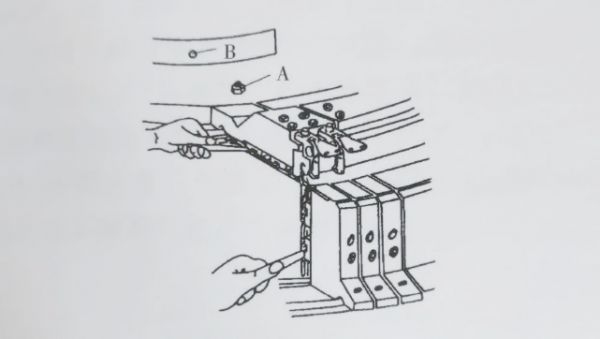
When installing the cambox, first carefully check the gap between each cambox and the cylinder (dial) (especially after the cylinder is replaced), and installing the cambox in sequence, so as to avoid the difference between some cambox and the cylinder or dial. When the gap between the cylinders (dial) is too small, usually a mechanical failure occurs during production.
How to adjust the gap between the cylinder (dial) and the cam?
1 Adjust the gap between the dial and the cam
As shown in the following picture , first, loosen the nuts and screws that are equally divided into six locations on the upper end of the middle core and the outer circle of the upper end of the middle kernel into three locations B. Then, screw in the screws at location A while At the same time, check the gap between the dial and the cam with a feeler gauge, and make it between 0.10~0.20mm, and tighten the screws and nuts of three places B, and then recheck the six places. If there is any change, repeat this process and know that the gap is qualified. until.
2 Adjustment of the gap between the cylinder and the cam
The measurement method and accuracy requirements are the same as the “adjustment of the gap between the dial and the cam”. The gap adjustment is realized by adjusting the cam pile positioning stop circle of the bottom circle of the circular cambox so that the radial runout to the center of the steel wire track is less than or equal to 0.03mm. The machine has been adjusted before leaving the factory and fitted with positioning pins. If the assembly accuracy is changed due to other reasons, the stop circle can be re-calibrated to ensure the accuracy of the clearance between the needle cylinder and the cam.
How to choose a cam?
The cam is one of the core parts of the circular knitting machine. Its main function is to control the movement and movement of the knitting needles and sinkers. It can be roughly divided into knit cam (loop forming) and tuck cam, miss cam (floating line) and sinker cam.
The overall quality of the cam will have a great impact on the circular knitting machine and the fabric. Therefore, pay special attention to the following points when purchasing the cam:
First of all, we must select the corresponding cam curve according to the requirements of different fabrics and fabrics. As designers pursue different fabric styles and focus on different fabrics, the cam working surface curve will be different.
Secondly, since the knitting needle (or sinker) and the cam are in high-speed sliding friction for a long time, individual process points also have to withstand high-frequency impacts at the same time, so the material and heat treatment process of the cam is very important. Therefore, the raw material of the cam is generally selected from the international Cr12MoV (Taiwan standard/Japanese standard SKD11), which has good harden ability and small quenching deformation, and the hardness, strength and toughness after quenching are more suitable for the requirements of the cam. The quenching hardness of the cam is generally HRC63.5±1. If the hardness of the cam is too high or too low, it will have an adverse effect.
Moreover, the roughness of the cam curve working surface is very important, it really determines whether the cam is easy to use and durable. The roughness of the cam curve working surface is determined by comprehensive factors such as processing equipment, cutting tools, processing technology, cutting, etc. (Individual manufacturers have extremely low triangular prices, and usually make a fuss in this link). The roughness of the cam curve working surface is generally determined as Ra≤0.8μm. Poor surface roughness will cause needle grinding, injection, and cambox heating.
In addition, pay attention to the relative position and accuracy of the cam hole position, keyslot, shape and curve. Failure to pay attention to these may have adverse effects.
Why study the cam curve?
In the analysis of the loop forming process, you can see the requirements for the bending angle: in order to ensure a lower bending tension, the bending angle is required to be hit, that is, it is best to only have two sinkers to participate in the bending, at this time the bending The angle is called the bending process angle; in order to reduce the impact force of the needle butt on the cam, the bending angle is required to be small. At this time, the bending angle is called the bending mechanical angle; therefore, from the different perspectives of process and machinery, the two The requirements are contradictory. In order to solve this problem, curved cams and relative motion sinkers appeared, which can make the angle of the needle butt contact with the came small, but the angle of movement is large.
Media Contact
Company Name: Morton Machinery Co., Ltd.
Contact Person: Media Relations
Email: Send Email
Phone: 0086-13004894622
Country: China
Website: https://www.mortonknitmachine.com/