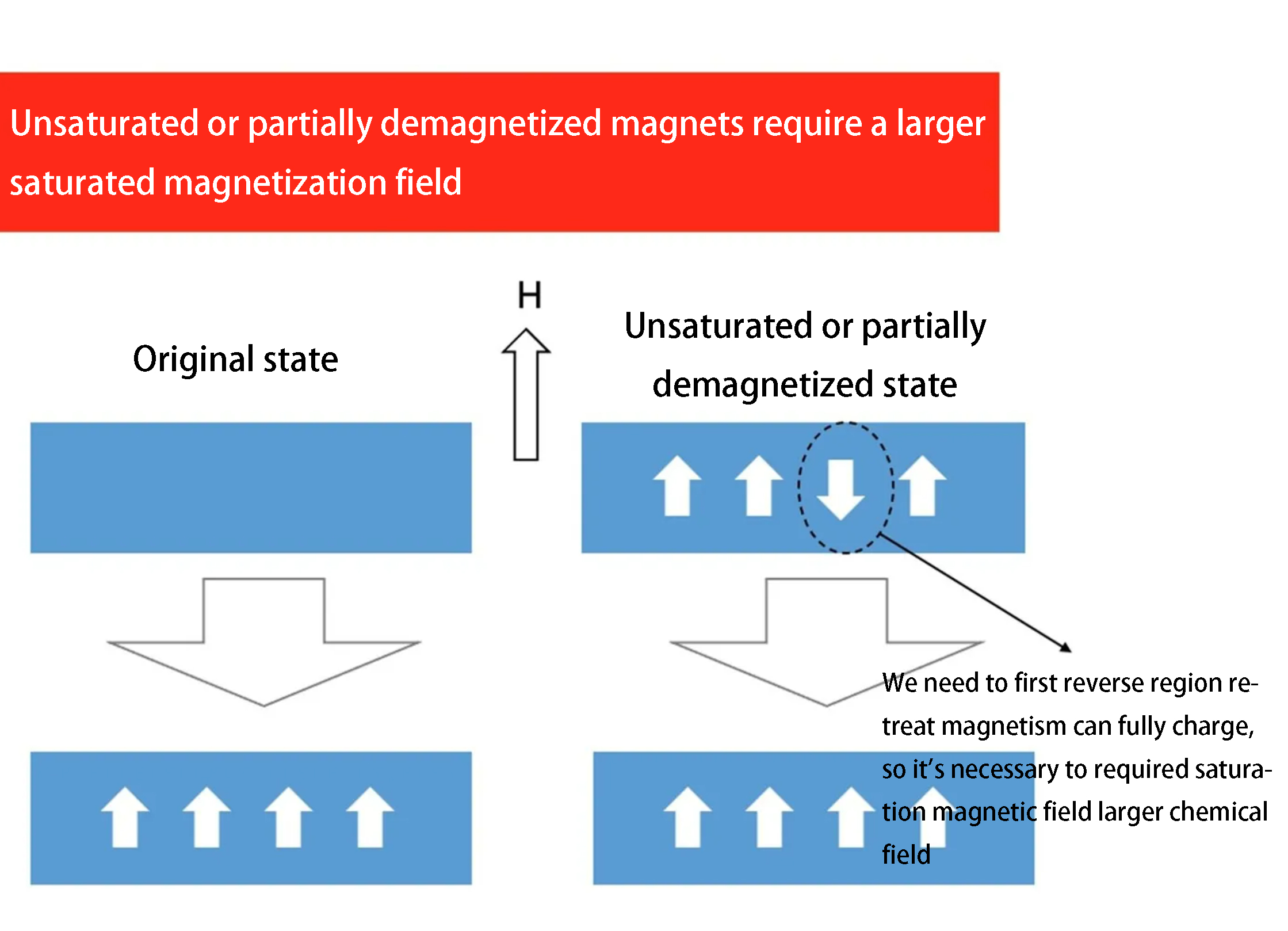

The magnetism of a magnet originates from magnetic order (where individual magnetic domains align in a specific direction). Sintered NdFeB is formed by compressing magnetic powder within molds. The process involves placing magnetic powder into a mold, applying a strong magnetic field using an electromagnet, and simultaneously exerting pressure with a press to align the easy magnetization axis of the powder. After pressing, the green bodies are demagnetized, removed from the mold, and the resulting blanks with well-oriented magnetization directions are obtained. These blanks are then cut into specified dimensions to create the final magnetic steel products according to customer requirements.
Powder orientation is a crucial process in producing high-performance NdFeB permanent magnets. The quality of orientation during the blank production phase is influenced by various factors, including the orientation field strength, powder particle shape and size, forming method, the relative orientation of the orientation field and forming pressure, and the loose density of oriented powder.

Magnetization is the final step to impart magnetism to sintered NdFeB.
After cutting the magnetic blanks to the desired dimensions, they undergo processes such as electroplating to prevent corrosion and become the final magnets. However, at this stage, the magnets do not exhibit external magnetism and require magnetization through a process known as “charging magnetism.”
The equipment used for magnetizing is called a magnetizer, or magnetizing machine. The magnetizer first charges a capacitor with high DC voltage (i.e., stores energy), then discharges it through a coil (magnetizing fixture) with very low resistance. The peak current of the discharge pulse can be extremely high, reaching tens of thousands of amperes. This current pulse generates a powerful magnetic field within the magnetizing fixture, which permanently magnetizes the magnet placed inside.
Accidents can occur during the magnetization process, such as incomplete saturation, cracking of the magnetizer’s poles, and fracturing of the magnets.
Incomplete saturation is mainly due to insufficient charging voltage, where the magnetic field generated by the coil does not reach 1.5 to 2 times the saturation magnetization of the magnet.
For multipole magnetization, magnets with thicker orientation directions are also challenging to saturate fully. This is because the distance between the upper and lower poles of the magnetizer is too large, resulting in insufficient magnetic field strength from the poles to form a proper closed magnetic circuit. As a result, the magnetization process can lead to disorderly magnetic poles and insufficient field strength.
Cracking of the magnetizer’s poles is primarily caused by setting the voltage too high, exceeding the safe voltage limit of the magnetizing machine.
Unsaturated magnets or magnets that have been partially demagnetized are more difficult to saturate due to their initial disordered magnetic domains. To achieve saturation, the resistance from the displacement and rotation of these domains needs to be overcome. However, in cases where a magnet is not fully saturated or has residual magnetization, there are regions of reverse magnetic field inside it. Whether magnetizing in the forward or reverse direction, some areas require reverse magnetization, necessitating the overcoming of the intrinsic coercive force in these regions. Therefore, a stronger magnetic field than theoretically needed is necessary for magnetization.
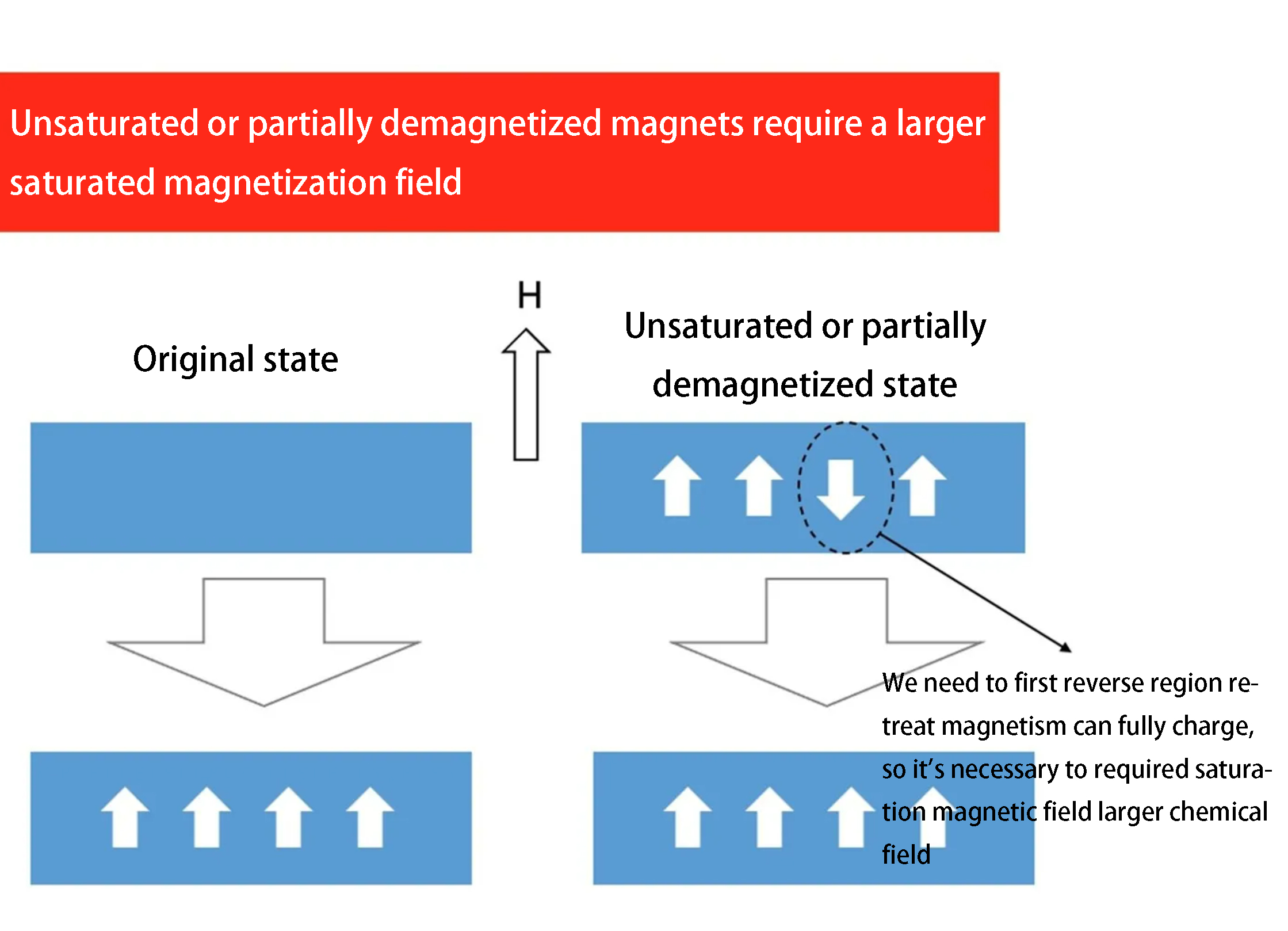
Media Contact
Company Name: Ningbo Honsen Magnetics Co., Ltd.
Email: Send Email
Country: China
Website: https://www.honsenmagnetics.com/