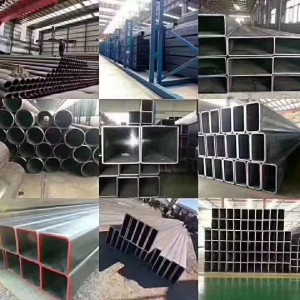
Hot dip galvanizing (steel tube) producer
Feeding → pickling, washing → solvent → drying → hot dip galvanizing → inside and outside blowing → rolling label, marking → passivation → inspection → packaging.
The loading worker shall check the material condition:
1. The outer surface of the steel pipe shall not be sticky with oil (especially oil stains such as asphalt oil blending paint), otherwise a large number of unqualified products will be caused.
2. The steel pipe must be straightened after production to eliminate the internal stress of the steel pipe.
3, the steel tube surface uneven corrosion can not be galvanized, otherwise a lot of hydrochloric acid will be wasted.
No artificial bending is allowed in the process of steel pipe transportation.
5. For hot-dip galvanized steel pipes, it is not allowed to stick marks on the inner and outer walls of steel pipes to avoid leakage plating.
1. Pickling of steel pipe:
1) Pickling workers must wear labor protection articles before work, carefully check whether there is barrier-free work site and whether the sling is intact, and then work can be carried out after confirmation.
2) Hydrochloric acid is mainly used in pickling, and hydrochloric acid is prepared by water. The content of hydrochloric acid is 18-20%, which is more appropriate.
3) Understand the acid concentration, temperature and the tonnage of the pickling pipe in the tank before pickling.
4) When lifting the pipe, the two slings should be about 1.3 meters away from the end, so as to avoid bending the steel pipe and causing leakage in the galvanized pipe;When going down the tube to the acid tank, the steel tube should be tilted 15°, so as to lower the standing end of the tube first, so as to prevent acid spray from injuring people.
5) Each pickling of steel pipe should be in weight of 2 ~ 5 tons and time of 5 ~ 15 minutes.
6) The steel tube should vibrate frequently during pickling. In the process of vibration, the steel tube should be placed on the horizontal stone of the acid tank, and the sling on one side should be started repeatedly for 3 times, and then the sling on the other side should be started again for 3 times, and then lifted after repeated twice;Vibration rise Angle is not greater than 15°.
7) When the acid tank is heated, fix the steam pipe firmly before opening the steam valve.
8) When the crane crane enters or leaves the acid tank, it shall not collide with the wall of the tank to prevent damage to the acid tank.
9) Main causes of under pickling of steel tubes:
(1) the steel pipe shall be strictly inspected when feeding, and the unqualified steel pipe shall not be put into pickling.
(2) The steel pipe is not operated carefully when it vibrates.
(3) Insufficient pickling time and hydrochloric acid content.
10) Main causes of steel tube pickling:
(1) Excessive hydroelectric acid content.
(2) Pickling time is too long.
11) After pickling, check whether the outer surface of the steel pipe is smooth, whether there is residual iron scale and whether the surface of the steel pipe is polluted by oil scale.
2. Water washing of steel tubes:
1) Water washing of the steel pipe should be carried out in a flowing clear water tank. Soak all the steel pipe in water when washing, relax the pickling sling and take off and off for three to four times.
2) After washing, the water inside the steel tube should be controlled and treated with solvent as soon as possible to prevent oxidation of the steel tube.
3) The content of iron and salt in the cleaning water shall not exceed the standard, and there shall be no other sundries. It shall be kept clean and transparent.
4) When cleaning the pipe, it is strictly prohibited for operators to step over the pickling tank to prevent slipping or falling into the tank to hurt people.
1. When the steel tube enters the solvent tank, loosen the sling so that the steel tube is immersed in the solvent completely. The surface of the steel tube is not allowed to expose the solvent surface. Until both ends of the steel tube are free of bubbles, one side of the steel tube shall be lifted up and down to vibrate, and the steel tube shall be lifted to control the clean solvent and then entered into the drying bench.
2. The tilt Angle of the steel pipe shall not be greater than 15° in the solvent treatment process.
3, the steel tube in the solvent immersion time of 60 ~ 120 seconds, the return tube immersion 3 ~ 5 minutes, the return tube immersion 5 ~ 10 minutes.
4. Solvent temperature: Keep the solvent clean at room temperature.
5. After the solvent treatment, do not stick to other dirt, do not get wet, put it into the drying table for leveling;People are not allowed to step on the steel pipe which is placed on the drying bench. If it must be stepped on, both feet must be coated with ammonium chloride before working on the pipe.
1. After qualified solvent treatment, put the steel tube on the drying and receiving platform, and put the steel tube on the front side of the zinc pot and the front side of the second magnetic roller to square at right Angle;The more curved pipe is placed in the back or straightened and placed on the receiving rack.
2. The main function of drying KANG is to dry the water on the surface of the steel tube. On the other hand, it is to raise the temperature of the steel tube itself, prevent zinc spattering from hurting people, and not take away the heat energy in the zinc pot, so as to accelerate the formation of zinc-ferroalloy layer.
3. The drying temperature of kang is 80℃ ~ 180℃, and the drying time of steel pipe is 3 ~ 7 minutes. The drying temperature can also be controlled according to the specifications and wall thickness of steel pipe.The dryers should check the drying degree of the steel pipe at any time to prevent the lack of time into the zinc liquid splash zinc injury;When drying, do not exceed the temperature, to prevent the solvent baking coke.The hot-dip galvanized steel pipe adopts the mechanical principle of dialing in, pressing down, spiraling, pulling out and lifting in the way of fully dipping semi-automatic galvanized steel pipe to complete the hot-dip galvanizing process.
1. Control of process parameters: The temperature of zinc solution should be controlled between 440-460℃; Zinc dipping time should be controlled between 30-60 seconds; Aluminium content (Zinc liquid level containing aluminium 0.01-0.02%)
2. Zinc ingot should be zN0-3 zinc ingot with national standard.
3. Maintain and control the reliable performance of the unplugging and pressing screw and unplugging lifting device regularly, strengthen the lubrication of the cylinder, adjust the height and Angle of the galvanizing pipe distributor well, and adjust the equipment to the optimal state.
4. Position the proximity switch accurately; Thermocouple line and meter to be used in the same model, otherwise, the temperature error is large, thermocouple protection sleeve, often check and replace.
5. The operator of the operating station shall manually adjust the speed according to the operation condition of the equipment in front of the furnace and the gesture command to prevent pipe sticking.
6. Preheat the tools used by the furnace workers before using them to prevent zinc spillage and injury; Frequently check whether the steel pipe falls into the pot, if any, to clear out in time;To timely adjust the equipment do not stick tube, to ensure the safety of equipment.
7. When adding zinc to the zinc pot, the zinc ingots should be preheated first. Never allow bundles of zinc to be added, no more than five pieces of zinc at a time.It is forbidden to drop iron into the zinc liquid to prevent a lot of zinc slag.
8, when melting zinc should be slowly heated, do not burn fire, otherwise it will damage the life of galvanized pot, and there is a lot of zinc vapor volatilization.When inhaled in excess, this harmful gas causes a condition called “foundry fever”. In the process of melting zinc, once the zinc has a high temperature must not touch the zinc block by hand, in order to avoid burns, should use appropriate tools to touch it.
9, to regularly clear zinc liquid surface of zinc ash. When scraping the ash should be gently on the surface of zinc liquid with the scraping plate scraping swab, can not stir too much, lest the zinc ash raised, the scraping plate should not be dipping zinc or out of the tube when the steel tube contact, so as not to roll over the occurrence of personal accidents or equipment accidents.
10. The zinc blocks on the ground in front of the furnace, broken zinc, zinc brought out when galvanizing, and the zinc steel pipe flowing to the outside should be recovered at any time to reduce the heat loss of the zinc pot.
11. When aluminum ingots are added to the surface of liquid zinc, it must be moved several times before and after to ensure uniform aluminum content on the surface of liquid zinc.
12. In order to facilitate waterlogging and zinc extraction, 20 tons of lead should be put into the inside of the zinc pot.
13, slag dregs to preheat the dregs, zinc slag to be divided into large and small blocks storage, the temperature of the dregs should be controlled at 455℃ above, swing slag machine must use special tools, away from the zinc pot 1 meter, feet to stand in a t-shaped.
14, hot dip galvanizing process requirements more rigorous, so in the hot dip galvanizing production process, must dry full station, that is to say, in unit time root number or tonnage more, the lower the cost, and vice versa higher. 1. After the galvanized pipe is put forward, magnetic roller table is used to lead out the galvanized pipe, and the revolution of the leading machine is not too fast, so that the zinc flows clean before internal blowing.
2. The Angle of the outer blowing ring should be parallel to the magnetic roller at right angles, and the longitudinal and transverse positions should be positive to ensure that the galvanized pipe passes through the middle of the wind ring.
3. When installing the magnetic roller, the five magnetic rollers must be on a center line to ensure the uniform zinc layer of the externally blown galvanized pipe.
4. External blowing shall be carried out with compressed air, preferably above 70℃, under a pressure of 0.2-0.4mpa.
5. Wind pressure shall be adjusted under the following circumstances:
(1) The zinc layer on the outer surface of galvanized pipe is too thick.
(2) The surface of zinc layer becomes dark after external blowing.
(3) After the external blowing, the surface of the zinc layer is adhered to sundries and strip unclean things. The air volume should be adjusted.
6. Replace the air ring of the same specification according to the specification of galvanized steel pipe. The air ring cannot be replaced by other specifications.
7. It is forbidden to pass galvanized pipe under the condition of no wind, so as not to cause blockage of air hole and affect the quality of external blowing.
8. Always check whether the inside of the outer blowing ring is clean, whether there is zinc hanging, whether the outside surface of the galvanized pipe is smooth and whether there is a scratch;Whether the surface of magnetic roller, chain is linked with zinc, if there is linked with zinc to clean up in time.
9. Since there is no magnetic roller and the zinc layer is not firm, the surface of the zinc layer is the most likely to be scratched, so the speed of the leading roller should match well with that of the magnetic roller. 1. The hot-dip galvanized pipe is sent to the side of the internal blower by the lead device, and the proximity switch is used to complete the horizontal movement, press down the internal blowing, raise the pressure head, and move the hot-dip galvanized pipe into the cooling sink.
2. The hot coated tube is the most likely to be scratched on the lead roller table. The main reason is that the zinc has not completely solidified during the operation of the tube.
3. Steam is used for internal blowing, and the internal blowing pressure is 0.4-1.0mpa; The inner surface of galvanized pipe must be smooth.
4, galvanized pipe in the chain to maintain a certain tilt Angle, so that the cooling water net.
5. The workplace of internal blowing is located in a steep place with a small working space, so it must be operated carefully to prevent slipping, falling and bending injuries; Strictly prohibit any part of the body, direct contact with high temperature galvanized pipe, so as to avoid injury.
6. Pay attention to whether your feet stand firm and there are other obstacles to prevent you from falling into the sink; It’s easy to leave the chain running on the sink, to prevent flying tube injuries.Meaning: When the parts need to be stored and transported for a long time, passivation should be carried out between the parts to prevent corrosion in the storage and transportation process. The corrosion products are often called white rust. Common passivation methods include chromate and phosphate.
1. Passivation method: hot-dip galvanized pipe is used to spray the passivation solution directly on the runway, and the solution is wiped off at a distance of one meter from the spraying position by steam knife. Be careful to blow off the passivation solution.
2. Wipe with compressed air to blow off the liquid on the surface of the steel tube and make the coating uniform. By adjusting the pressure to adjust the thickness of the coating, no excess beads should be attached to the surface of the zinc tube. 1. Rolling mark and roller:
1) When the marking machine is working, do not touch the marking roller with your hand to prevent hand pressing; It is forbidden to pass the double pipe through the marking machine to prevent the damage of the press roll.
2) During the operation of the galvanized pipe in the conveying roller table, the marking machine shall change the note according to different specifications, and the height of the press wheel shall be adjusted once the specifications are changed, and oil shall be added frequently.
3) The rubber ring of the rolling marking machine should be frequently checked and replaced in time if any crack is found.
4) The rubber wheel shall be pressed on the center line of the steel tube, and the upper and lower fixing bolts with good pressure Angle shall be adjusted.
5) When printing the logo ring, two people should roll at the same time. Ink should be added frequently to roll the steel pipe with felt, but ink is not easy to be too much.
2. Packaging:
1) The baler USES air compressor gas, and the pressure is 0.4-0.8mpa.It is forbidden to touch the moving parts of the baler with your hands to avoid hurting your hands under the working condition of the baler.
2) When packing, first put the buckles on the packing belt, then put the packing belt around the steel pipe and insert the other end into the buckles. Then press the baling machine on the packing belt and open the air valve of the baling machine for packing and pressing.The thick part of the packing belt is 1.0-1.2mm. The packing belt is required to be 100mm away from the end, 300mm away from the second part, and 400mm away from the end of the blue bar mark.
3) Choose the packing rack of the same specification for the galvanized pipes, put the galvanized pipes into a hexagonal shape and make one end even.
4) Once the outer surface of the packed steel pipe causes pollution, clean it with clean cotton sand before stacking. If conditions permit, the water inside the small pipe should be controlled and cleaned;Do not allow anyone to step on the tube with his foot, to maintain the appearance of galvanized tube quality.
Tianjin Rainbow Steel Group is a professional steel product manufacture in China.
The product we can manufacture as below:
Our Main Product Range:
1. Steel Pipe (Round / Square/ Special shaped/SSAW)
2. Electrical Conduit Pipe (EMT/IMC/RMC/BS4568-1970/BS31-1940)
3. Cold Formed Steel Section (C /Z /U/ M)
4. Steel Angle and Beam (V Angle Bar / H Beam / U Beam)
5. Steel Scaffolding Prop
6. Steel Structure (Frame Works)
7. Precision Process On Steel (cutting, straightening, flattening, pressing, hot rolling, cold rolling, stamping, drilling, welding, etc. According to customer’s requirement)
8. Steel Tower
9. Solar Mounting Structure
Our Company Advantage:
1. Price: Our Company is located in Tianjin China. For decades, Tianjin has been the steel industry center and the largest steel pipe production base in China. The industry chain of steel and metal products is complete; It has a large material and labor resources here. So the steel pipe types made in here is very complete , the quality is super , the price is very advantageous. AS a group company, our four factories can get a more favorable price of raw materials due to the large purchase quantity of single batch of materials. The prices of export products are all intro-group prices, so we have a price advantage over other independent exporters.
2. Transportation: Our mills are only 70km away from Tianjin Port, which is the Largest port in north China, with vessels ship to more than 300 ports in 170 countries. Our company is only It’s very Convenient and saves both time and cost in transportation.
3. One stop service: As a group company, we have four mills with a modern warehouse & processing facility, we can supply you with an extensive range of steel products: hot rolled and cold formed, including a wide variety of merchant bar, structural and tubular products. We have all the domestic, commercial and industrial steel supplies and services you could possibly need. So if you purchase from us, what we can provide is a one-stop steel product service. It saves much of your purchasing time and sourcing cost.
4. Product Capacity and delivery: We have a large production capacity, and export more than 3500 tons per week (nearly 150 20 GP containers),We can delivery the goods Within 20-30 days after receiving T/T deposit or L/C. For special urgent orders, we can shorten the leading time to 10 days.
5. Manufactured according to different standards, Meet different standards:
Since our products have been exported to many different countries and regions like Europe, America, Australia, Africa, Asia etc. , our products can meet the requirements of different national standards. If you have special requirements, just tell us, we can produce customized products for you, not only meet your quality requirements, but also save you cost a lot.
Our experienced and knowledgeable staff is always ready to answer your questions about our products and services.
Media Contact
Company Name: Tianjin Rainbow Steel Group Co., Ltd.
Contact Person: Media Relations
Email: Send Email
Phone: 0086-13920397257
Country: China
Website: https://www.tjrainbowsteel.com/