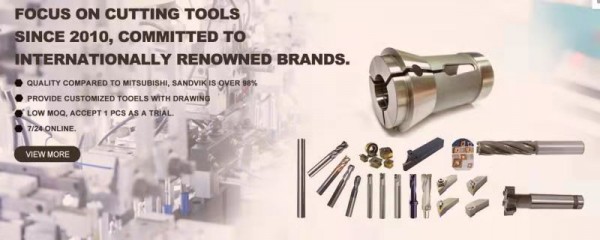
There are several factors to consider when deciding which fixture is more effective. All of the following factors need to be taken into account when deciding between a collet chuck and a chuck jaw chuck for a given lathe task.
1、Spindle load capacity
The maximum permissible weight of a lathe spindle is based on the bearing load capacity and if the weight of the chuck and workpiece combination is too great, the bearings may be overloaded. For machining tasks where there is a danger of exceeding the limits, this danger may dictate one’s choice of workholding. Jaw chucks tend to be heavier than the equivalent collet chuck, so where weight control is required, a collet chuck is the appropriate choice.
2、Spindle speed
Collet chucks are often the better choice when turning at very high spindle speeds, for two main reasons.
One reason relates to the quality of the chuck, assuming the same spindle horsepower is used to drive the jaw chuck and collet chuck, a heavier jaw chuck will take longer to accelerate to the required speed and the longer acceleration time will lengthen the work cycle and reduce productivity.
Another reason relates to centrifugal force as it increases with the squared value of rpm, so this value is important in the case of high speed cutting. For example, doubling the spindle speed will result in four times the original centrifugal force. This force pulls the chuck jaws away from the centre and tends to reduce the clamping force. With a collet chuck, however, the centrifugal force does not have a significant effect. As a result, the clamping force is more stable over the entire machining speed range.
3、Machining operation
The collet chuck applies the clamping force around the entire circumference of the part, not just in selected contact areas, thus achieving good concentricity, which is particularly important for secondary machining projects, where the accuracy associated with primary machining needs to be taken into account, as the collet chuck’s high accuracy clamping capacity allows the collet chuck to be used for secondary machining even when the chuck jaws are used for primary machining. A chuck with hollow soft jaws can achieve a repeatability of TIR (total reading) in the range of 0.0006 to 0.0012 inch, while a collet chuck has a typical repeatability of 0.0005 inch TIR or better. To further improve secondary machining accuracy, the concentricity of the collet chuck can also be adjusted during the installation process.
4、Workpiece size
The collet chuck is ideal for workpieces less than 3″ in diameter. In particular, the collet chuck limits the axial (Z-axis) travel range of the machine, as it is longer than the chuck jaws. When the length of the workpiece requires almost the entire available travel of the machine, a jaw chuck will probably be used.
5、Lot sizes
Collet chucks are suitable for both very large and very small batch sizes.
The advantages of collet chucks for small batches and multiple tasks are related to the product changeover time, which can take around 15 to 20 minutes for a standard jaw chuck, 1 minute for a specialised quick change jaw chuck, and 15 to 20 seconds for a quick change collet chuck.
When machining large batches, the same clamping-related time savings can be accrued. Collet chucks require less opening and closing time than jaw chucks, reducing cycle times by reducing non-cutting time from one workpiece to the next.
6、Workpiece size range
Part of the reason for the faster opening and closing of the collet chuck is its shorter drive stroke, which allows a more limited range of workpiece sizes to be used in collet chucks than in jaw chucks.
7、Sub-spindle situation
Turning machines with sub-spindles are often used for a variety of high-volume machining applications where collet chucks offer significant savings in machining time. They can machine all sides of a part in a single work cycle and these machines are often combined with bar feeders for unattended production and continuous machining of workpieces. In these applications, the time saved in chuck drive time may be small for a single part, but over the entire production process, the time saved per part multiplied by the number of parts machined can add up to significant time savings.
8、Chuck tool library
When one is choosing a suitable workholding device between a chuck jaw chuck and a collet chuck, it is also important to consider a third option. Where possible, keeping both fixtures and changing from one to the other can be a very cost effective solution. Changing from a jaw chuck to a collet chuck, or vice versa, usually takes less than 20 minutes. Jaw chucks can be retained on the machine to deal with the uncertainty of the part range. However, when the machine is machining large batches of workpieces, or several batches of uniformly sized parts, the productivity gains gained by using collet chucks greatly outweigh the lost productivity due to the time spent changing fixtures.
In fact, the speed of a collet chuck is flexible and if the workpiece dimensions are consistent, the collet chuck will be faster. If there is a large variation in workpiece size, a chuck jaw chuck may be required to accommodate workpieces with a wide range of dimensions.
9、Type of material
For hot rolled steel, forgings and moulded parts, standard jaw chucks tend to be more effective because of the inherent variation in diameter of all such parts. On the other hand, parts made of cold rolled materials tend to have better dimensional consistency and are therefore suitable for collet chucks. However, the lack of consistent diameter measurements does not necessarily constitute an obstacle to the use of collet chucks, and chucks designed for non-circular cross-sections are available for holding moulded bar stock in the shape required by the customer.
CN CNC TOOLS are focus on Produce Lathe Collet/ Guide Bush/ Bar Feeder/ Sleeve etc for more than 10 years and 100% following 173E Collet and many engineers are from them. So they are quality will be reach Europe Standard.
Media Contact
Company Name: CN CNC TOOLS
Contact Person: Jacky Wang
Email: Send Email
Phone: +86 14714816052
Address:Floor 1, Shixi Industrial area, Canton
City: Shenzhen
State: Guangdong
Country: China
Website: https://www.cncnctools.com/